3D modelling
The best 3D modelling in the region for one-off products, prototypes, production parts, constructions, assemblies, series, spare parts, innovative products, and others. We will lead you along the path from model to prototype.
Unique. Flexible Quick.
Like a puma.
What is 3D modelling to us?
3D modelling is of paramount importance to us. We feel an obligation to check or advise in such a way that the models are properly prepared so that they can be produced in the best quality. Whenever we take responsibility for a 3D model, we guarantee the 3D drawing. This means that we guarantee that the product is suitable for production, irrespective of the technology used. The more complicated the product, the more attention we pay to the model. But if you already have your own model, we’ll look at it and see if it can be optimised even further.
For us, the word ‘impossible’ doesn’t exist. So far, we’ve turned every single model into a prototype. The first thing we always ask you is what the prototype is going to be used for. If we see that there are ways of producing it more affordably, we’ll draw your attention to that fact.
3D modelling with the touch of puma. We bring speed, responsiveness, and integrity to the fore in the way we go about our business. We respond to 3D production by way of the PUMA method which enables a holistic approach to the resolution of problems, uniqueness, minimising costs, and maximising success as well as proactivity in business.
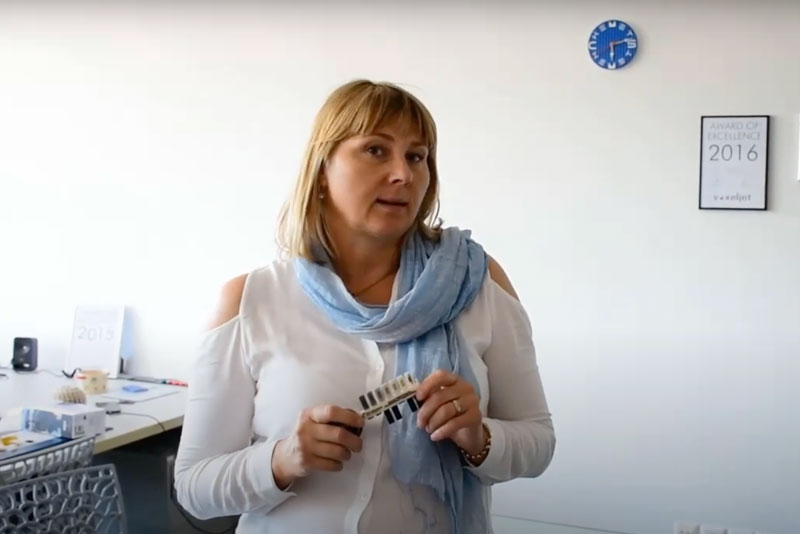
What is 3D modelling in prototyping?
3D modelling is the digital visualisation of your ideas. 3D modelling is also called 3D drawing, or 3D designing. This means that we turn the idea in the form of a drawing, photo, or sketch into a 3D digital format. We turn two-dimensional images into three-dimensional forms. We do this by using dedicated computer software.
A 3D modelled product is a 3D model. Three-dimensional models represent a physical shape by way of points in a 3D space. These points are connected to many geometric forms, such as triangles, lines, curves, and the like. 3D models are created manually, by using algorithms, or by scanning.
3D models are most prevalent in 3D graphics and in CAD, or Computer-Aided Design. From there, they found their way into 3D printing. An expert, who does 3D modelling has the role of a 3D designer, a 3D planner and/or a 3D constructor. It is perfectly normal that he takes on all three roles at the same time.
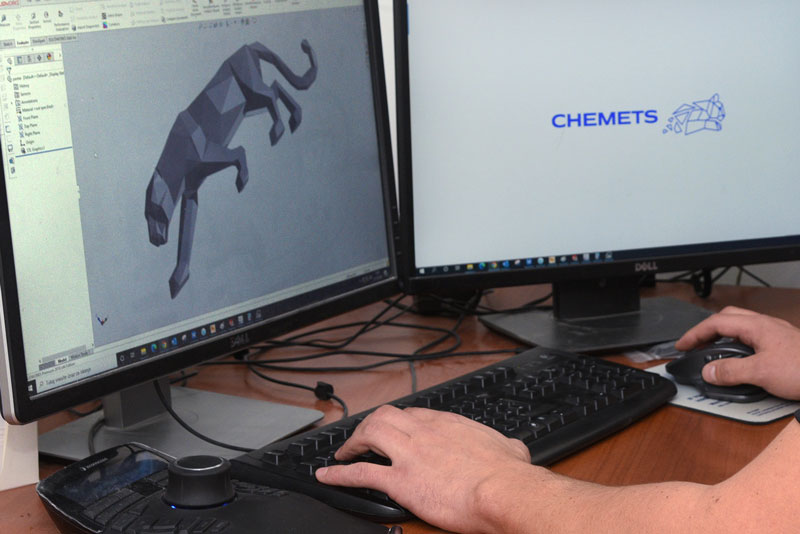
In 3D printing, what is the difference between 3D modelling and 3D design?
In prototyping, 3D modelling and 3D design are two expressions that are very closely related to each other.
The result of a 3D design is a 3D render. The result of 3D modelling is a 3D model. With the modelling process, we find our way to the first prototype.
If we look at things a little more closely, a 3D designer does not have to design 3D products himself, but he can coordinate with, and guide, a 3D constructor. A 3D constructor is the one who actually develops the 3D model in the computer program.
3D modelling, visualisation, and scanning in 3D printing
3D visualisation is the display of an idea in action. In 3D printing, it is used for more demanding technical projects or innovations, where the visual presentation of the final product is important. It is most commonly used in 3D printing in the fields of architecture and construction.
A 3D expert for 3D visualisation is called a 3D visualiser. He is a 3D expert whose task is to bring the idea or desired product to life. It is either an architectural sketch or a plan of the building. The 3D visualiser creates an animation of the building, which includes individual elements made with the help of 3D printing.
3D scanning is also associated with the development of 3D visualisation. It comes into its own when it is necessary to collect data from existing products, facilities, or surfaces. These days, it is necessary to collect more and more data for the creation of quality prototypes, with even more details, and sometimes also even on a larger surface area. And it is 3D technologies that allow us to capture the necessary data for 3D modelling.
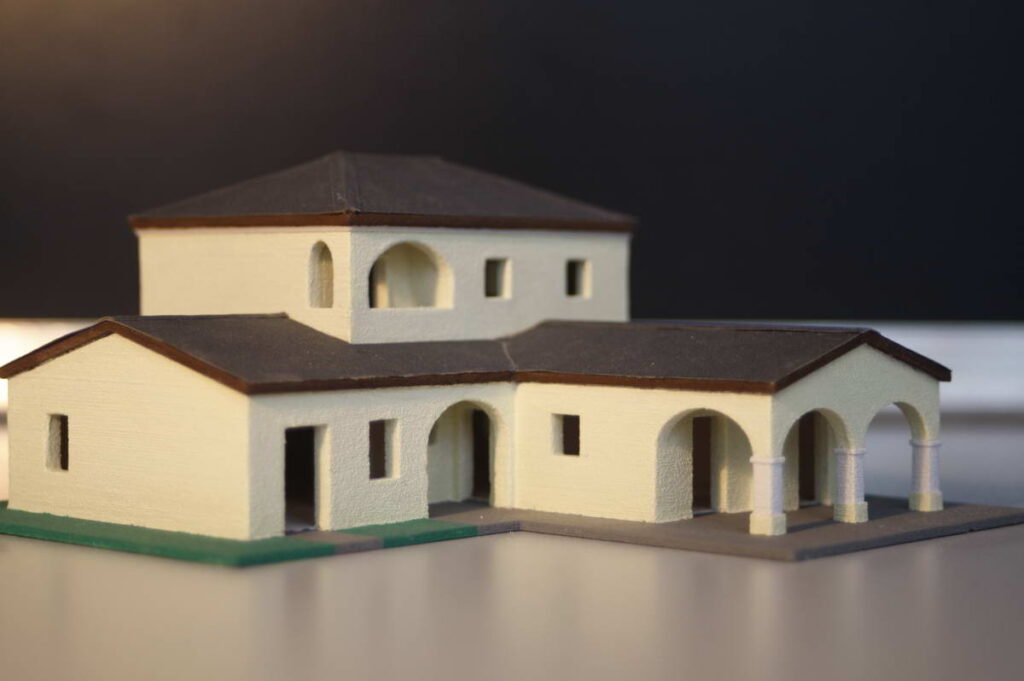
Types of 3D modelling
The most common types of 3D modelling include 3D forms based on polygons such as pyramids, cubes, spheres, cylinders, and cones, as well as smooth, defined shapes along frame curves. From a computational perspective, these are quite complex.
3D models can be classified into two categories: A solid: these models determine the volume of the object they represent (like a rock). A shell or a border: these models represent the surface, that is the boundaries of an object, not its volume (like an infinitely thin eggshell).
In 3D printing, solid models are the ones that are mostly used. Modelling solids and shells can create identical objects, from a functional point of view. The differences between them are mainly in the way they are created and set up as well as the possibilities of their use in different fields, including differences in the types of approximations between the model and reality.
3D modelling approaches
With 3D modelling, the same results (3D models) can be created using different techniques. Each option has its own advantages and disadvantages. That is why it is advantageous knowing as many techniques as possible and to adapt the choice of technique to the type of model. This can often save us a lot of time or improve the accuracy and detail of the model.
The oldest, and most common approach is the build-out or edge-by-edge approach. Polygon modelling involves manipulating one of the basic component parts, usually a cube or sphere, and then using basic operations to displace and divide the surfaces (source: Wikipedia).
There are two other approaches: using NURBS curves (Non-Uniform Rational Basis Spline), which are mathematically defined curves determined by order, the set of weighted (or unweighted) control points, and the knot vector and the digital sculpture, a method which is very similar to traditional sculpture. With the assistance of various tools, the designer transforms one of the basic components, typically having a large number of polygons, giving him a great degree of control over processing the shape. (source: Wikipedia)
Topology in 3D modeling
In 3D modelling, we also take care of topology. Topology is the optimisation of a material within the boundaries where the material is located. Mesh topology indicates the way in which the 3D model has been constructed and shows how the polygons are arranged and interconnected.
Topology optimisation is increasingly becoming a necessary component, especially in designing load-bearing structural parts. If engineers want to be successful and up to date with the latest, they must, in addition to using all other forms of knowledge, use state-of-the-art tools for the design of complex products as well as take into account the efficiency of production and subsequent use.
In the field of developing optimised methods, by far the most important at the moment is optimisation topology of load-bearing mechanical parts. Namely, topology optimisation can, compared to other optimisation procedures, bring about the most benefits. To get a quote for topology optimisation, simply ask us.
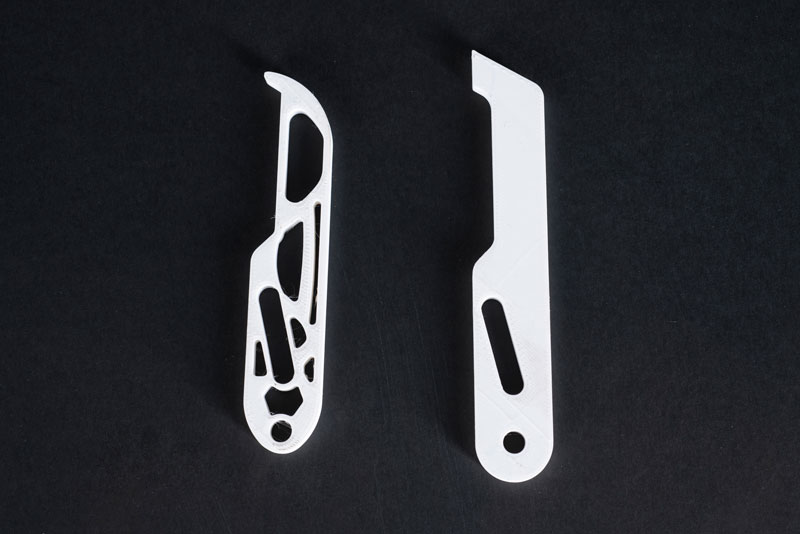
How long does it take to produce a 3D model and what is the price for its preparation?
The production of a 3D model falls within the first phase of prototyping. The time required for the production of a 3D model depends on the quality of the delivered data as well as the drawing. The starting point can also be a photograph or a physical product (for example the bumper of an old-timer car). The more information the 3D constructor has, and the clearer the picture about the product, the faster he can estimate the cost of making the model and the faster he can complete the first 3D model.
At Chemets our advantage is that we have a lot of experience in 3D modelling, as witnessed by the 500 or so projects we take care of on a yearly basis. We are a partner of Voxeljet, our German partner company, that is the leading producer of 3D industrial printers in Germany.
The price for preparing a 3D model is individualised for each individual client and project. In the case that you are interested in a quote for 3D modelling, it is best that you contact us for a price and details of when we are able to make this happen for you.
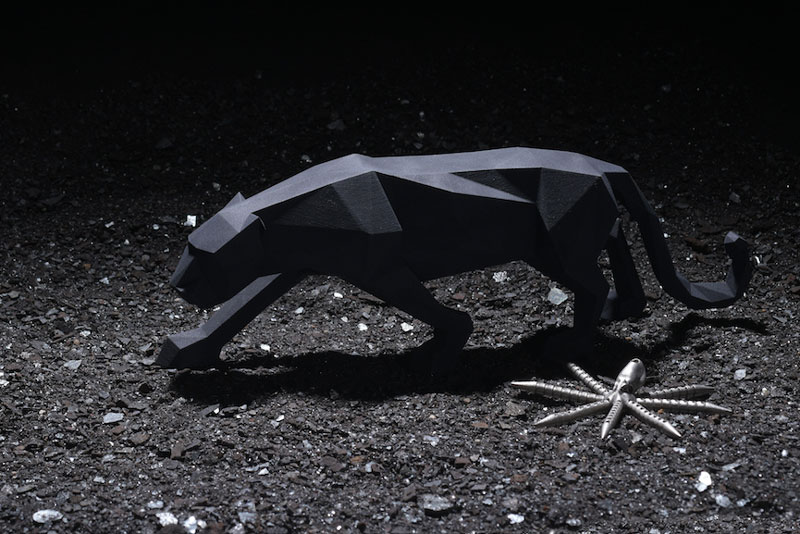