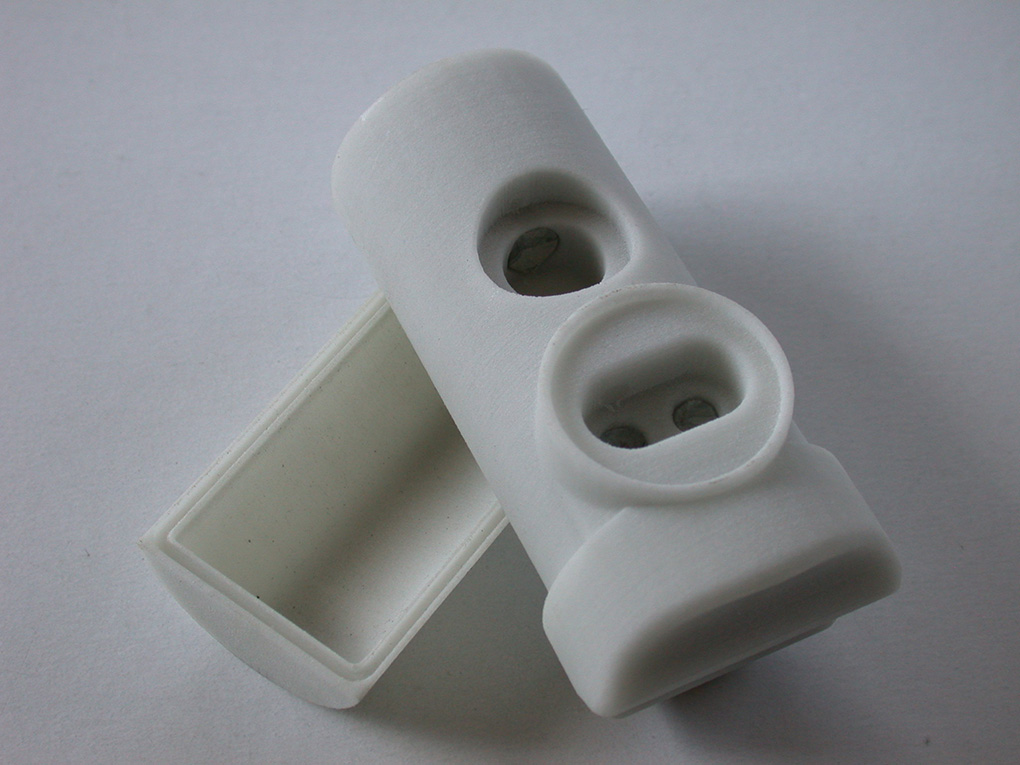
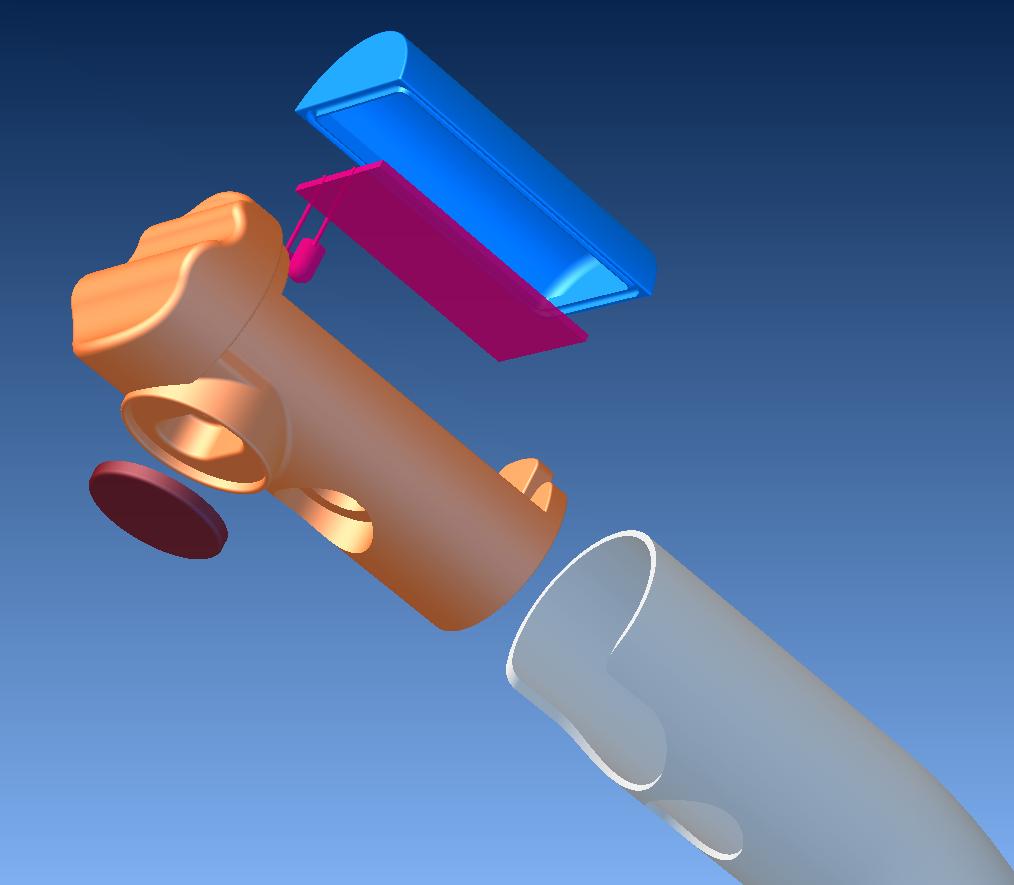
The VS Group company, upon following world trends and introducing new technical elements into sensor activated plumbing fixtures, decided for the development of new plumbing fixtures. Given that technical elements found in sensor activated plumbing fixtures are constantly changing, the need for new construction methods and also the design of plumbing fixtures showed itself to be necessary. Sensor activated plumbing fixtures are today really small electronic products; electrical parts are becoming all the more smaller, are battery activated and valves are half the size they were a few years ago. Taking all this into account, the decision was made, for new plumbing fixtures. In the first phase, the idea was to develop a completely new composite plumbing fixture, which was implemented during the design phase, above all due to the newly awaited arrival of electronic valves onto the market.
The plumbing fixture is comprised of formed stainless steel, an insert, electronic parts, LED sensors, batteries and a sensor cover. The fundamental demand was that the insert itself be waterproof, and at the same time acts as a holder and enables the flow of water.
With this in mind a solution was sought for the simple closing of the part of the insert, in which an electronic part is located. With this function the insert / plumbing fixture obtained a new element, a sensor cover, which has a dual function. The outer appearance of the insert obtained a new feature, which monitors the waves of water as they exit the fixture. In the same manner, the waves influence the sensor function of the fixture, the new feature of the insert therefore combines a number of different functions.
Given the demands of the insert itself, with all perforations and details, as well as the outer appearance, it was very clear early on that such an insert would not be able to be produced with existing technological processes. For the requirements of small series production it would have been possible to produce the insert using classical tooling technology, but with regard to fact that the insert was already constructed in a CAD format, the only sensible and correct way forward was via CNC machining or 3D printing.
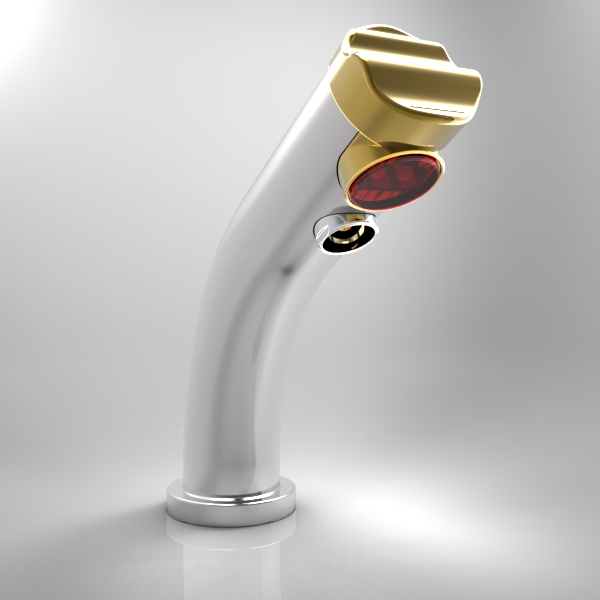
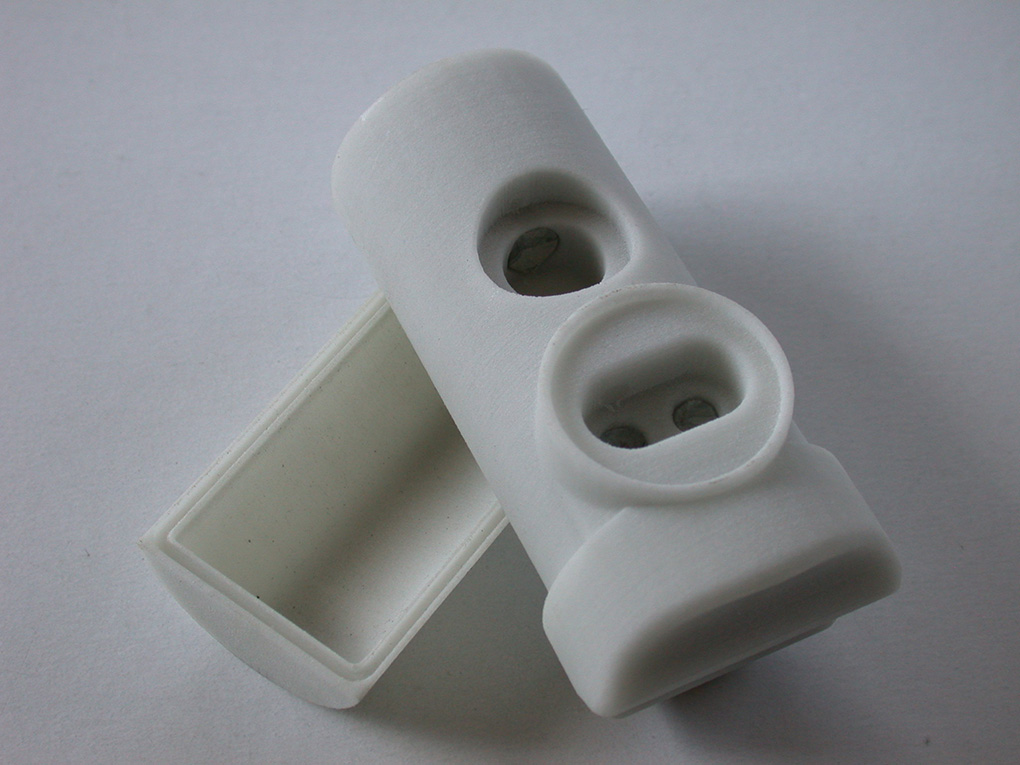
At Chemets we produced the first models using SLS 3D print technology. Another possible 3D print was the use of Polyjet technology, however that direction was disregarded due to the nature of the product itself and the surface demands with regard to quality. During the next phases, with the use of silicon moulds, identical copies of the 3D print were made, which were used for the adjustment and checking of the shape of the stainless steel tubing as well as the in the development of the product itself and preparation of production. The move to digital technology enabled the VS group company to check the situation as to the dimensions of the product as it went, to adjust the parameters of elements and to eliminate classical tooling stages. This modern digital manner of design and production of prototypes in this case has shown itself to be faster and cheaper in the sense of simplifying processes and the quality of them.