As a design engineer or development engineer, you know that choosing the right manufacturing technology is crucial for the success of your project, especially when dealing with serial production. Among the most commonly used techniques for making plastic and rubber parts are injection molding and vacuum casting. Recently, 3D printing has also become an option, but this article will focus on injection molding and vacuum casting. We will explore the key factors that will help you choose the right technology or tool for your project based on the size of the series.
Injection molding: ideal technique for large-scale production
Injection molding is an excellent choice for large-scale production of complex parts with high consistency. Here are some key points to consider:
- Material: Precisely define the material you will use for your parts. Suitable material ensures the durability and functionality of the final products.
- Design: Ensure that the design of your parts is optimized for injection molding. Complex designs may require additional planning but offer better functionality and aesthetics.
- Quantity: Estimate the projected annual production quantity. Injection molding becomes cost-effective for large series due to the low cost per part.
Certifications and market conditions: Check which certifications are required for your product and what the conditions for market entry are.
Vacuum casting: flexible solution for small to medium-scale production
If your project requires smaller quantities or prototype production, vacuum casting may be the right choice. This technique offers greater flexibility and lower initial costs. Key points include:
- Flexibility: Vacuum casting allows for easy adjustments to material and design, making it ideal for iterative prototype development.
- Initial Costs: Compared to injection molding, the initial costs of vacuum casting are lower, as expensive tooling is not needed.
Speed: Preparation of tools and production of smaller series are faster, allowing for quick delivery and adaptability.
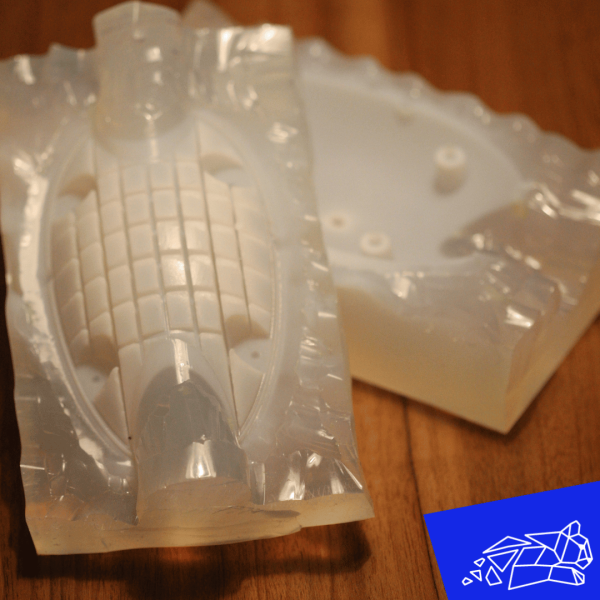
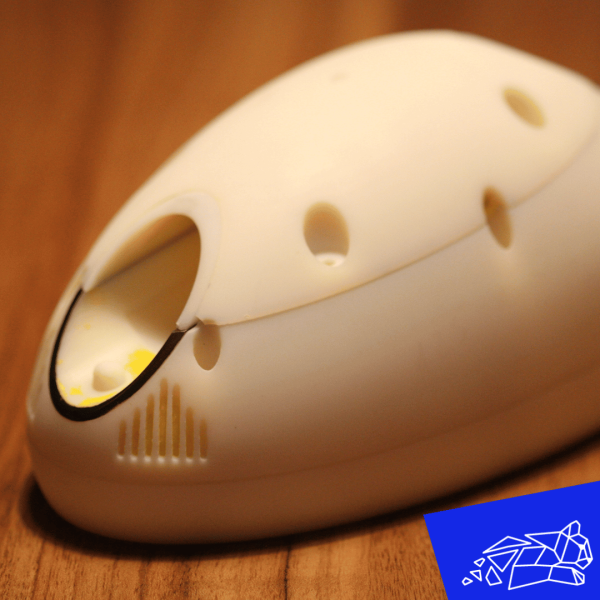
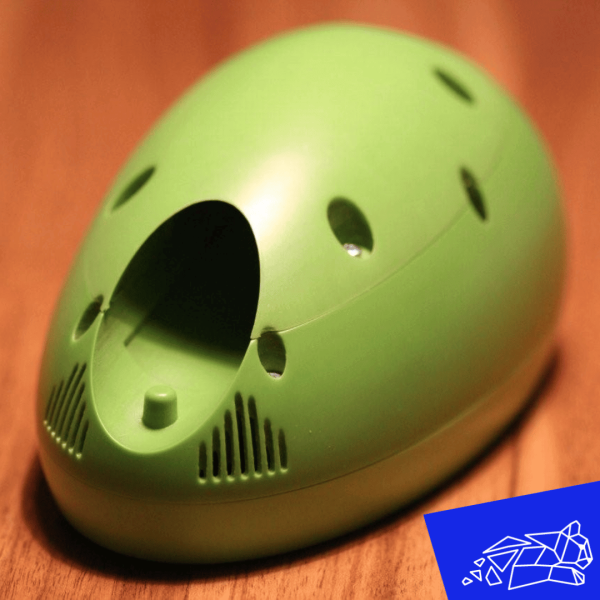
Suitability of Production Scale
When choosing between injection molding and vacuum casting, it is important to consider the production scale:
- Injection Molding: Ideal for large-scale production (from thousands to millions of parts), as it ensures high repeatability and consistency.
Vacuum Casting: Suitable for small to medium-scale production (1 to 100 parts) and is an excellent choice for prototype and small series production. Ideal technology when additional casting is required.
When to Choose Which Technique?
- Injection Molding: Best suited for products where there is a requirement for large-scale production. Commonly used in the automotive industry, consumer goods, and medical devices.
- Vacuum Casting: Ideal for prototypes and small series production. Often used in product development, product testing, or market testing during the time required to produce injection molding tools.
Statistical Analysis: Economy of Scale and Cost Efficiency
A study by the National Institute of Standards and Technology (NIST) showed:
- Injection Molding: Achieves economies of scale at quantities above 1,000 parts, with significant cost reductions as quantities increase.
Vacuum Casting: More cost-effective for quantities under 100 parts or castings (when using a multi-core mold), with fast lead times, making it suitable for rapid prototyping and small series.
How to Decide Between Injection Molding and Vacuum Casting?
The choice between injection molding and vacuum casting depends on the specific needs of your project:
- Injection Molding: Optimal choice for large-scale production with long-term cost efficiency.
- Vacuum Casting: Provides the necessary flexibility for small production volumes and prototype creation without significant upfront investments.
When deciding, consider factors such as:
- Production volume (projected annual quantity)
- Time constraints (required production time)
- Material properties (required technical data sheets, certifications, etc.)
- Overall project budget (how much you are willing to invest at each stage of product development and production).
Choosing the right technology will ensure the success of your project and achieve the desired results.
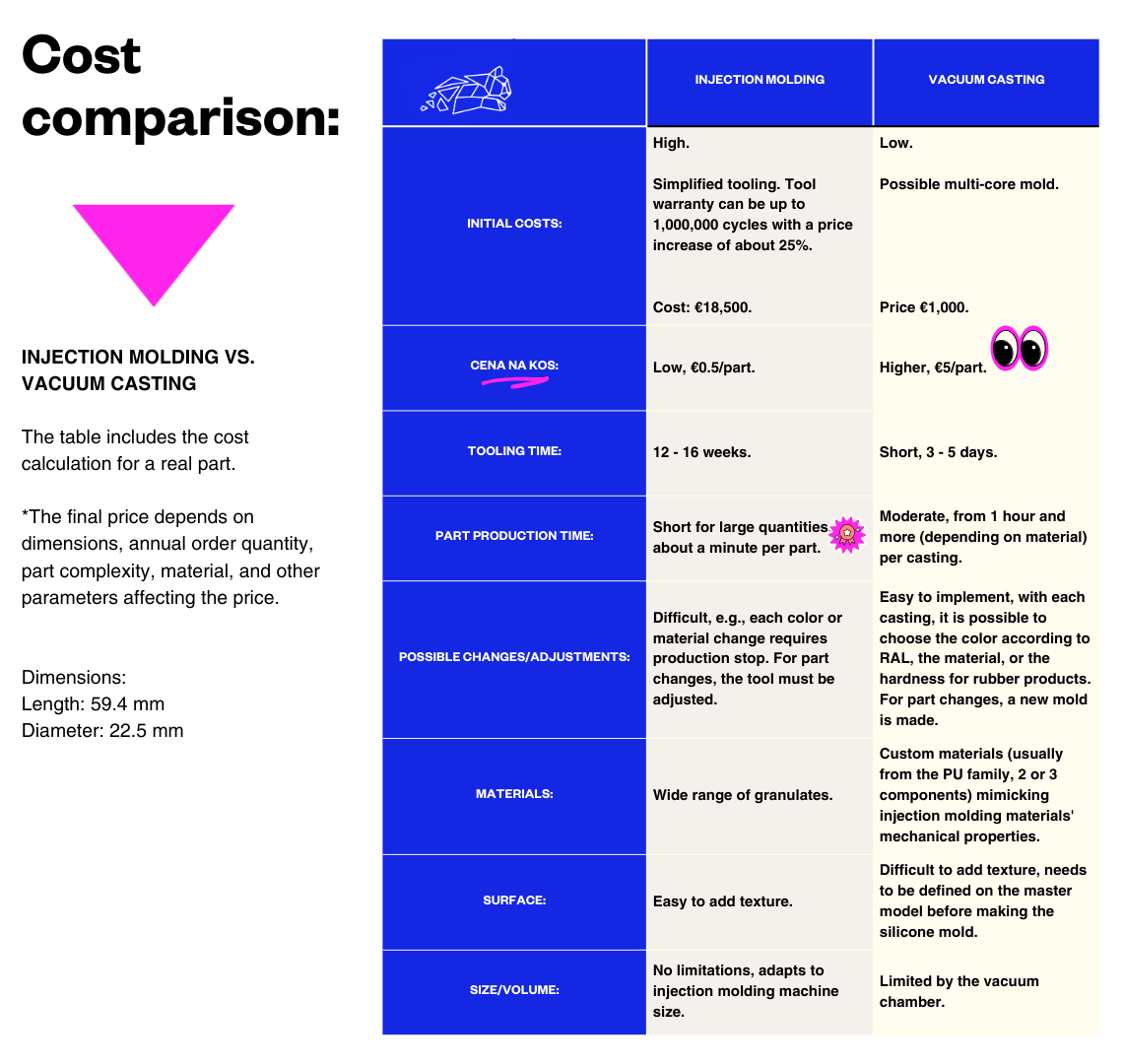
Need Expert Advice?
We assist with proposals or execution, from material selection to product optimization. We simplify it by considering your requirements, needs, and desires, aiming to reduce manufacturing costs and optimize your investment with the correct choice of manufacturing method or technology.
If your criteria for a specific product and series allow for 3D printing (additive manufacturing), we can provide a financial assessment to help you decide whether to use external 3D printing services or implement a 3D industrial printer in your production process.