Prototyping: investment or expense?
When developing a new innovative product, it is necessary to follow guidelines that determine the sequence of steps in this process: from setting goals, the level of financial investment, the business activities of the company to analysing and testing the product.
The new product must be thoroughly scrutinised, otherwise it may turn out to be indistinct, have too few advantages, and will not be accepted by the market. To push forward development and at the same time avoid large financial and time-based losses, it is necessary to test the product at all stages of development before production begins, and so we often need a prototype.
In the product development phase, it is safer to invest in the production of prototypes and the first small series with 3D technologies, rather than the production by way of tooling and test injection moulded pieces. The latter option is more expensive and also requires more time.
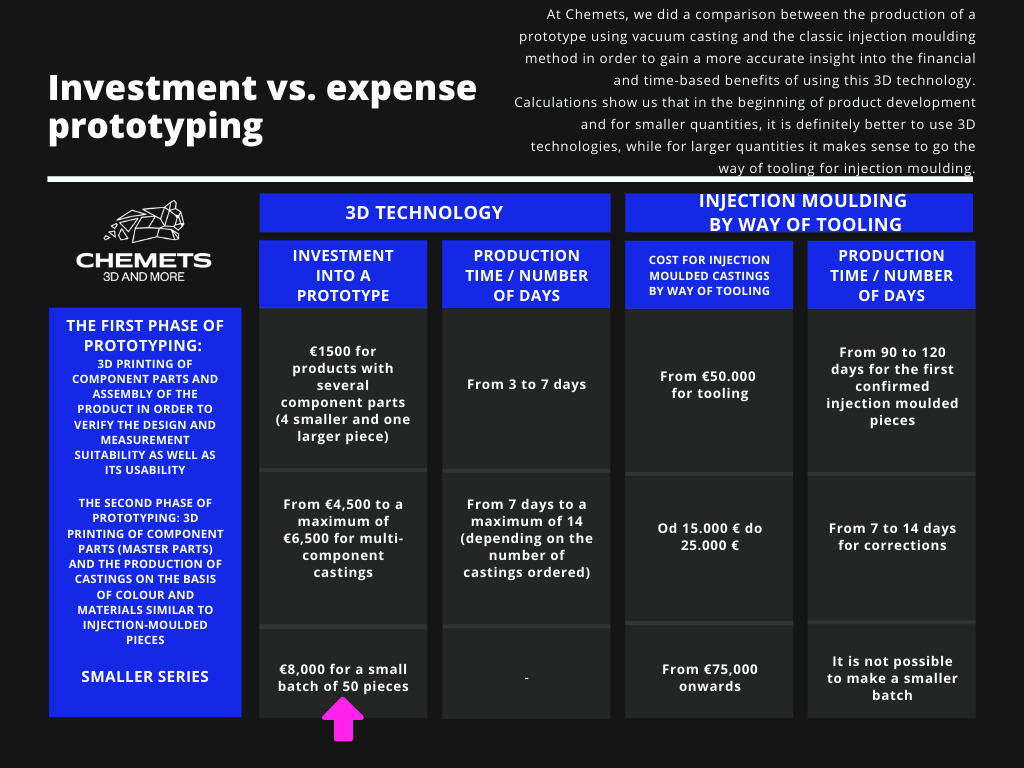
1. The path from presenting an idea to producing a prototype
The client has a good idea and a computer drawing of the product
The client presents his idea and the characteristics of the product he wants. Many times the product has already been drawn up ad is in the 3D STL file format. If not, we do it.
Determining the investment cost for the production of a prototype for testing purposes
The usability of the new product, its design, and measurement suitability must be tested. With a prototype that has been produced, the product can be actually tested. Typically, clients at this stage want the financial investment to be as low as possible and for the prototype to be produced as quickly as possible. Choosing 3D technology for prototyping is therefore completely logical.
The prototype production process
After consulting with the designers of the new innovative product, we look for the most suitable method of production in the first phase of prototyping. In doing so, we take into account the size of the product, the number of components, the technical properties of the material, and the desired production time. We recommend the selected 3D printing technology according to the testing requirements, eg: testing the shape, measurement suitability, functionality, technical properties of the material, etc.
Checking the parameters and repeat prototyping
After checking the parameters of the product or only a certain part of the assembly, a certain phase of testing is repeated until the whole assembly meets all the required parameters. It is recommended that the construction and drawings are done by a constructor who works closely with the industrial designer and prototype manufacturer from the early stages of the product design, as it is then possible to take into account the things that are crucial to its production.
“When you don’t have the financial resources, go ahead but do it step-by-step. Pay attention and ask the market. “
This is honest advice that we at Chemets give to clients who are developing new products. They are typically financially limited in terms of the development of a new product, while at the same time they do not have feedback from the market on whether the product will be interesting or not.
In the second phase of the development of a product, and an important period of testing as well as obtaining valuable information from the market, minor corrections are usually required on individual parts or even on all parts of the product. At this stage of the development of a new product, all that is known is that sales cannot be predicted in advance and it is necessary to be cautious. To avoid excessive financial losses as well as too much time, we recommend making smaller series’.
Possible ways of making prototypes and small series’ for testing the market
There are several ways, but we will focus on two for making a prototype and a small series where the appearance of the finished pieces by way of vacuum casting is almost identical to injection moulding, and the materials are close to the original ones.
- with injection moulded pieces from tooling or
- the production of vacuum castings
What is the difference between them?
When producing injection moulded pieces by way of tooling, the price per piece is lower and therefore this method of production is suitable for the production of large series’. With vacuum castings, the price per piece is higher, but it is possible to make just 1 piece and a smaller number of products, which is definitely enough to test the market.
Making large batches at a stage when the market has not yet been tested is out of the question, as the product may not be sold or improvements may be found to be needed. The company may be left with stock on hand that represents a cost and they might not be able to sell them.
3. Price per piece or the end amount for a small batch?
We advise our clients not to look at the lowest price per piece, but the lowest end amount for testing 1 piece or a small batch, as well as the speed of production. With 3D technologies, the product can be produced in as little as a week. The whole process of producing a prototype and a small series in the traditional way is from a financial and time perspective more complex as well as time-consuming, especially when we look at the production of tooling.
At this stage, we at Chemets recommend the production of at least three castings, or sets. Of these, one is for the client, one for the seller, and the third for a potential customer.
4. A financial and time-based comparison between prototyping with 3d technology and injection moulding
At Chemets, we did a comparison between the production of a prototype using vacuum casting and the classic injection moulding method in order to gain a more accurate insight into the financial and time-based benefits of using this 3D technology.
Calculations show us that in the beginning of product development and for smaller quantities, it is definitely better to use 3D technologies, while for larger quantities it makes sense to go the way of tooling for injection moulding.
Regarding the complexity of a product and its added value, it depends on whether such a method of production enables earnings, already in the prototyping phase. Sometimes we can even cover our own product costs by way of small batches. Usually, such manufacturing is just a way to enter the market with minimal costs.
Advantages of producing plastic prototypes by way of vacuum casting
- The prototypes are of high quality.
- In appearance and with regard to their technical properties, they are very close to final series products.
- A wide range of materials allows for the production of functional, as well as useable products.
- 3D technologies allow for the development of a product based on a single piece, all the way to complex assemblies.
- The biggest advantage is the possibility of making just one product or a small batch.
Prototypes are suitable for mechanical testing, presentations, promotions, as well as obtaining certificates …
Have a great prototyping.
Barbara H. Wilkesmann