At Chemets, we are most fulfilled by projects where technology is not just a tool—it tells a story. One such project was our collaboration on the sculpture for the Rado Smerdu Award—the highest national award for achievements in the field of nature conservation.
When Technology Becomes a Messenger
At Chemets, we are often approached by clients with demanding technical challenges, but sometimes, we get to work on projects that truly touch our hearts.
That’s how Urh Wiegele reached out to us—he participated in a public competition to design the sculpture that would symbolize the Rado Smerdu Award. This new national award recognizes outstanding contributions to nature conservation. It was first presented in 2024 and was this year awarded at the Nature Day 2025 celebration at Brdo.
The winning sculpture is not just an artwork—it tells a story about the cycles of life, the interconnection between nature and society, and the idea that every element in the world is part of something greater.
The Artist’s Vision: The Infinite Connection of Nature
Urh Wiegele summarized his concept in a powerful message:
“Nature is a system of inseparable connections, with neither a beginning nor an end. Everything is connected. Everything depends on everything else.”
His sculpture, shaped as an infinite loop, perfectly embodies this idea—a delicate balance and interdependence. The mirrored surface invites the observer into the story and becomes part of an active dialogue between art, nature, and humanity.
The sculpture is not stable. That’s precisely its strength. Even the slightest movement can disturb it—just as even the smallest intervention can affect the balance of natural ecosystems.
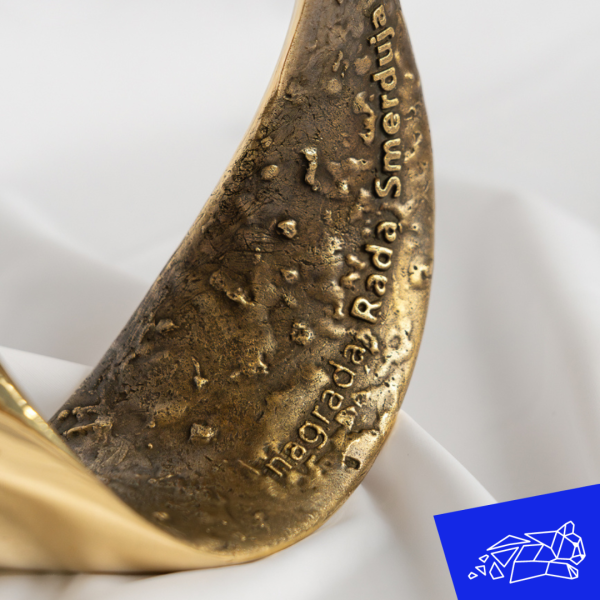
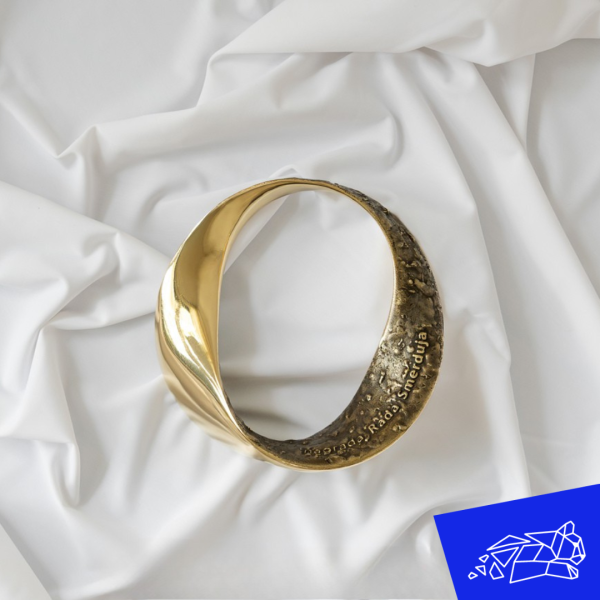
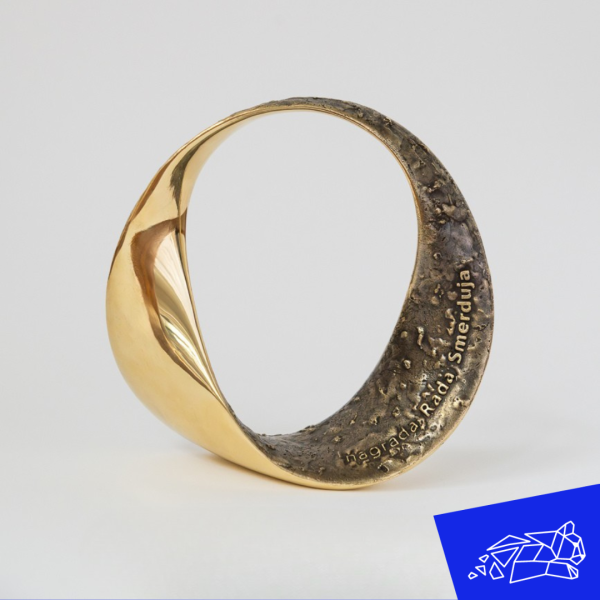
When Art Meets Technology
At Chemets, we approached this project with complete sensitivity to the idea. The sculpture required technical adaptation—we were in constant contact with the artist to optimize every detail.
Since one part of the sculpture was quite thick, we hollowed it out internally. This prevented potential defects during printing, reduced production time, and lowered material costs. We chose SLA technology and used iSquared resin, for which we have exclusive representation.
The 3D printed model served the client as the base for casting the final bronze sculpture. Since we are well-versed in various casting technologies, we can prepare models, molds, or cores for our clients in a way that ensures the final product is optimal in appearance, production, and function.
After printing, we completed the full post-processing chain:
✔️ Cleaning the print and removing supports
✔️ UV and thermal curing
✔️ Hand sanding in multiple stages to achieve a perfectly smooth surface
The timeline? Exceptionally short. From design confirmation to final delivery, the sculpture was completed in just three to four days.
A Partnership That Matters
When Urh informed us that his sculpture had won the competition, it was a moment that truly filled us with pride. Projects like this remind us why we do what we do.
If you are looking for a partner who understands your artistic vision and can bring it to life with technical precision—we are here for you.